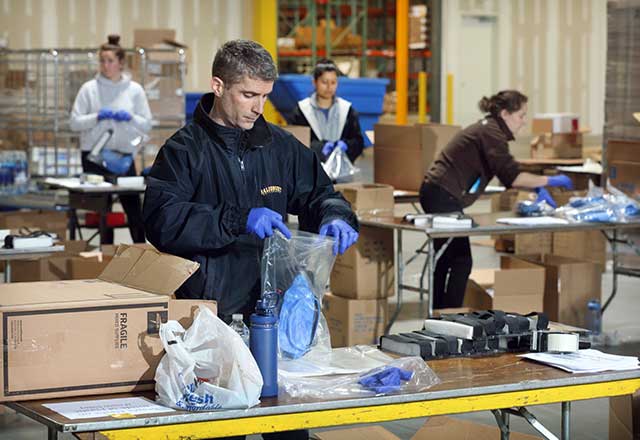
Posted March 29, 2020 | Written by Karen Nitkin
In normal times, Isabel Lake would be in school.
Instead, the second-year Johns Hopkins medical student sits in a large room in the Johns Hopkins Consolidated Services Center, the offsite warehouse that the health system opened in 2018.
She’s measuring and cutting straps for face shields that will help protect Johns Hopkins health care workers from coronavirus infection.
“Our classes were cancelled, so we were looking for something to do and ways to help out,” says Lake, who arrived at the storage facility with fellow students Joe Broderick and Lyla Atta. Like others in the warehouse, they are abiding by physical distancing rules and sitting at least six feet from each other as they work.
The medical students are among dozens of Johns Hopkins volunteers who are either creating the face shields or assembling personal protection packs that will help clinicians reuse their surgical masks and N95 filtering respirators.
Each personal protection pack holds a face shield, two brown paper bags, a marker, alcohol-based hand sanitizer containing at least 60% alcohol and a surgical mask. Clinicians add their N95 respirators.
The volunteers are taking part in an extraordinary push to make 50,000 such kits for all Johns Hopkins clinicians in Maryland and Washington, D.C., as cases of COVID-19 continue to rise.
“This is about preserving the supply of personal protective equipment,” says Michelle Azotea, who created the improvised production system in her role as director of project management and implementation for the health system.
Clinicians rely on the masks and respirators to protect themselves from infection, typically discarding them after a single use.
But masks and other personal protective equipment (PPE) have been in short supply for several months, starting with a manufacturer recall in December, says Burton Fuller, vice president, chief supply chain officer for the Johns Hopkins Health System.
The situation worsened in January when the Chinese manufacturers of PPE stopped production so workers could stay home, part of a campaign to halt spread of the novel coronavirus in that country.
“We have a perfect storm of fluctuating supply, surge in demand and high degree of difficulty getting additional products,” says Fuller. “Therefore, we are implementing important steps to preserve our PPE.”
One such step has been limiting the number of people who can enter a patient’s room to treat, observe or socialize — a decision that means fewer masks get used.
Another is to create face shields that protect the masks for future use.
“I just felt like I needed to do something,” says one volunteer, oncology research nurse Lesley Donoho-Cohen, as she cuts straps. “The supply of masks is critical to health care provider safety.”
A Scaled Up Arts and Crafts Project
One day in mid-March, Fuller handed a commercially made face shield to Azotea. He wanted to know if Johns Hopkins could make 50,000 of them. Quickly.
The idea came from Polly Trexler, director of operations for Hospital Epidemiology and Infection Control (HEIC) at The Johns Hopkins Hospital, and Melanie Curless, HEIC’s assistant director of operations. They had made similar mask-protecting shields when volunteering overseas years ago, says Fuller.
Azotea sat at a conference table, studying the shield. She noticed the elastic at the back, the strip of foam that held it tight to a wearer’s forehead. She mapped out how Johns Hopkins could make its own version.
“I’m fairly crafty,” she says. “It took two or three hours to figure it out. It’s a fun challenge to scale up an arts and crafts project to this size.”
Supply chain staff members spent several hours on March 14 making a first round of shields. After the shields were approved by HEIC, the next challenge was securing sufficient shield-making supplies.
A Supply-Chain Solution, Right Down the Road
Azotea searched online and found the foam for forehead protection, the netting for straps and the elastic that holds the shield in place. But she still needed a supplier for the thin plastic that would form the protective part of the device. She found the solution right down the road, on Pulaski Highway.
Total Plastics International, based in Michigan but with locations around the country, was ready to take on the challenge. “This is a fairly large order for us,” says Sandy Young, a sales representative for the five-employee Baltimore site. “We ordered more materials and our guys worked last night until 8, and they’ll work this weekend,” she said on March 20.
Powered by Volunteers
Volunteers have been streaming to the Johns Hopkins supplies warehouse on Holabird Ave. in Baltimore to help. About 250 volunteered in the first week, making between 2,000 and 6,000 face shields per four-hour shift, says Fuller. By March 24, more than 25,000 shields had been made.
Many of the volunteers learned about the effort from Kevin Sowers, president of the Johns Hopkins Health System and executive vice president of Johns Hopkins Medicine, who described the project on his Strengthening Ties blog and included a link to sign up.
“We are experiencing an unprecedented time in our history as a global society, and it will take innovation and, most importantly, teamwork, to navigate these unchartered waters,” Sowers wrote. “Thank you to all involved in this creative endeavor.”
If you are a student, staff member or employee of Johns Hopkins Medicine or Johns Hopkins University, you can click here to register to volunteer.
Work stations in the large and well-ventilated room are more than six feet apart, and the space is continually sanitized. A maximum of 25 people can volunteer at a time, and they must attest that they have no fever or respiratory issues.